Project Profile: Five Star Dairy Farm
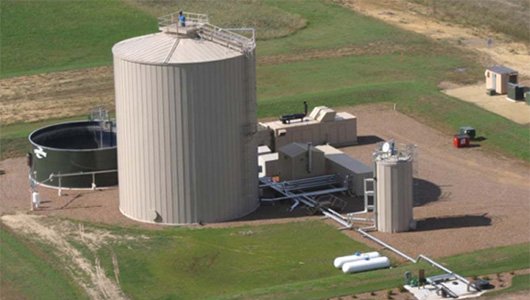
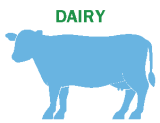
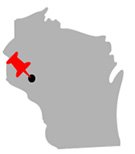
Key Features
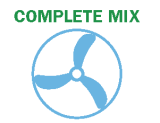
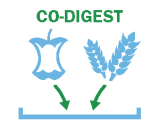
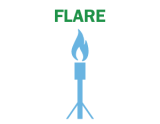

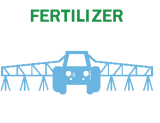
Highlights
- Sold biogas for electricity generation from 2005 through 2014
- Installed biosolids dryer for manure digestate in 2017
- Herd health and milk production improved with the use of dried bedding, which reduces infection risk
The Jensen family founded Five Star Dairy in 2000. Taking inspiration from an anaerobic digestion (AD) system in Minnesota, the dairy installed its own AD system in 2005 and began selling biogas for renewable electricity generation to the local utility.
Overview
“It really reduces odor (and methane emissions) of the manure, and it’s another income stream.”
– Lee Jensen, Five Star Dairy
Operational since 2005, Five Star Dairy’s above-ground, thermophilic, complete-mix digester operates at a target temperature of 125°F. A scrape system collects manure three times per day from the barns, and every half-hour, the digester accepts a batch of manure mixed with about 10 percent off-site food waste, which the dairy stores in an above-ground, cylindrical tank adjacent to the digester. The co-digested organics include high fat wastes such as oil and grease, which enhance biogas production and are integral to the system’s design.
From 2005 to 2014, Five Star had an agreement with Dairyland Power Cooperative, an energy service provider based in western Wisconsin and covering over 44,000 square miles. Dairyland bought Five Star’s biogas and operated an on-site 775-kW engine-generator set to produce electricity. This agreement served as a business model for similar projects at Norswiss and Wild Rose Dairies. In 2014, Dairyland Power bought out the contract. The generator at Five Star has been offline since, and the dairy has been flaring its biogas.
Digestate Use
Despite the halt on electricity production, Five Star Dairy still benefits from the digester through the production of bedding for its cows. Five Star originally used sawdust bedding in the stalls, but the digested manure solids provided an opportunity to switch to deep bedding without having to make the expensive transition to sand bedding. The farm installed its first manure screw press separator in 2006 and installed a second separator years later. The separators run 24 hours a day, accepting manure in slurry form. Liquid digestate goes to a storage pit to be used as fertilizer, and solids exit the separators at 70 percent moisture and a rate of 50 to 100 pounds per minute. The solids then pass through the farm’s triple pass rotary drum bedding dryer, manufactured by McLanahan Corporation and installed in late 2017.
Five Star installed the dryer hoping that a lower moisture bedding would increase milk quality and lower the occurrence of mastitis in the cows. The dryer runs 10 to 12 hours per day. Conveyor belts move manure solids from the separators to the dryer’s hopper, which is designed to evenly feed solids into the dryer and dry them efficiently. The bedding spends three to four minutes in the dryer, which operates at temperatures up to 1,000°F, before being discharged at 142°F. This results in a moisture content of 45 percent and greatly reduces the pathogens in the final bedding.
Since Five Star started using the dryer in 2017, milk production has improved from an average of 89.9 pounds to 96 pounds per cow. Decreased pathogens in the bedding have contributed to improved herd health as cases of mastitis have decreased, leading to decreased antibiotic use. The increased milk production helps cover the cost of running the separators and dryer, and the Jensen family feels that the benefits outweigh the cost.
Five Star trucks the liquid digestate to spread on remote crop fields and applies it to nearby fields using drag hoses. The dairy also uses separated solids on fields that require extra phosphorus. They have three nutrient management plans to maintain their fields, and they believe that their soil health has improved significantly due to using digestate.
Looking Forward
At the time of Dairyland Power’s buyout in 2014, it was difficult to make biogas-to-electricity projects profitable, due to decreasing electricity costs. However, other avenues are now available for increasing the profitability of anaerobic digestion, such as renewable natural gas production. Five Star Dairy is exploring options for upgrading their biogas to compressed natural gas for vehicle fuel, which will be a more cost-beneficial outlet for the biogas than electricity generation in the current market.
Benefits
Five Star Dairy has advanced sustainability in the following ways:
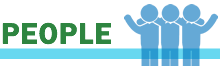
- Improves quality of life in the community by reducing odor
- Reduces pathogens through anaerobic digestion of manure
- Enhances farm image among community members

- Improves soil health through the application of nutrients in liquid and solid digestate
- Reduces methane emissions from livestock manure
- Improves herd health and leads to decreased antibiotics use
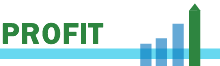
- Generates revenue from the sale of compost
- Reduces operating costs by using bedding product on site
- Generated revenue from sale of biogas to utility for electricity generation before generator went offline
System Design Properties
Property | Value |
---|---|
Feedstock Processed | Dairy cow manure |
Throughput | 90,000 gallons per day |
Digester type | Complete mix |
Population Feeding Digester | 1,100 dairy cows |
Baseline System | Storage lagoon |
System Designer and Developer | Microgy, Inc. |
Biogas Uses | Electricity (through 2015); flare |
Digestate Use | Bedding and fertilizer |
Recognition
The Dairy Business Association (DBA) selected Five Star Dairy to receive the 2010 DBA Environmental Excellence Award. This award was developed to recognize a Wisconsin dairy producer in honor of its outstanding waste and pollution prevention projects that protect Wisconsin's natural resources.
Want to learn more?
Find more information about Five Star Dairy operations in McLanahan’s case study, at https://www.mclanahan.com/resource-library/five-star-dairy-manure-bedding-dryer-case-study, and in this 2020 interview with Lee Jensen: https://www.youtube.com/watch?v=No-hVo5NY_s.
Pursuant to 5 CFR § 2635.702(c)(2), names are displayed here as the result of recognition for achievement given under an agency program of recognition for accomplishment in support of the agency’s mission. Any reference to a specific company or commercial product or service by trade name, trademark, manufacturer, company, or otherwise does not constitute or imply the endorsement or recommendation of EPA. Reviewed December 2021