Release Prevention for Underground Storage Tanks (USTs)
On this page:
Introduction
In 2015, EPA revised the underground storage tank regulations. Below you will find new requirements for spill protection, overfill protection, and corrosion protection.
- How can UST releases be prevented?
- What is spill protection?
- What is overfill protection?
- What are correct filling practices?
- What is corrosion protection?
How can UST releases be prevented?
The U.S. Environmental Protection Agency designed part of the technical regulations for underground storage tank systems to prevent releases from USTs. The regulations require owners and operators to properly install UST systems and protect their USTs from spills, overfills, and corrosion and require correct filling practices to be followed. In addition, owners and operators must report the existence of new UST systems, suspected releases, UST system closures, and keep records of operation and maintenance.
- UST technical regulations
- Properly install UST systems
- Report existence of new UST systems
- Keep records of operation and maintenance
What is spill protection?
Spill protection is containment around the fill pipe that catches small drips or spills that occur when the delivery hose is disconnected from the fill pipe. This containment is typically called a spill bucket. It may also be referred to as a catchment basin, or spill containment manhole. Basically, a spill bucket is a basin sealed around the fill pipe. To protect against spills, the spill bucket should be large enough to contain what may spill when the delivery hose is uncoupled from the fill pipe. A typical delivery hose can hold about 14 gallons of fuel. Spill buckets range in size from those capable of holding only a few gallons to those that are much larger--the larger the spill bucket, the more spill protection it can provide.
You need a way to remove liquid from spill buckets. Manufacturers may equip spill buckets with either a pump or drain to remove liquid. Or you can purchase a spark free hand pump. You should try to keep your spill bucket clean and empty. Some spill buckets can collect enough water and sediment, along with spilled product, to make draining this mixture into the tank unwise. If this happens, you may pump out the spill bucket and dispose of the liquid properly. If the liquid contains fuel or chemicals, it could be considered a hazardous waste. Contact your implementing agency responsible for hazardous waste for information on testing and handling requirements.
Note: If an UST never receives more than 25 gallons at a time, the UST does not have to meet the spill protection requirements. Many small used oil tanks fall into this category.
2015 Requirement – Not later than October 13, 2018, spill buckets must be either double walled (with periodic monitoring of the integrity of both walls of the spill bucket) or tested periodically for proper operation according to the new spill prevention equipment testing requirements.
What is overfill protection?
Overfill protection devices either shut off product flow, restrict product flow or alert the delivery operator with an alarm when the tank is close to being full. These devices are installed inside the tank and activate if the product in the UST reaches a certain level in the tank. Typically, your UST must have overfill protection. The three types of overfill protection devices are:
- Automatic shutoff devices
- Overfill alarms
- Flow restrictors (also called ball float valves)
Note: If an UST never receives more than 25 gallons at a time, the UST does not have to meet the overfill protection requirements. Many small used oil tanks fall into this category.
2015 Requirement – Not later than October 13, 2018, overfill prevention equipment must be inspected periodically for proper operation according to the new overfill prevention equipment testing requirements.
What are correct filling practices?
Many releases at UST sites come from spills and overfills that occur during delivery. Although these spills are usually small, repeated small releases can cause big environmental problems. To help prevent spills and overfills during tank filling, the UST regulations require owners and operators to meet the following correct filling practices:
- Volume available in the tank is greater than the volume of regulated substance to be transferred to the tank before the transfer is made
- Transfer operation is monitored continuously
Industry standard practices are also available for tank filling.
What is corrosion protection?
Unprotected underground metal components of the UST system can corrode and release product through corrosion holes. Corrosion can begin as pitting on the metal surface. As the pitting becomes deeper, holes may develop. Even a small corrosion hole can result in significant releases over time. In addition to tanks and piping, metal components can include flexible connectors, swing joints, and turbines. All metal UST system components that are in contact with the ground and routinely contain product must be protected from corrosion. The two common methods used for protecting metal components from corrosion are cathodic protection and isolating the metal component from the corrosive environment.
All USTs installed after December 22, 1988 must meet one of the following performance standards for corrosion protection:
- Tank and piping completely made of noncorrodible material, such as fiberglass-reinforced plastic.
- Tank and piping made of steel having a corrosion-resistant coating and having cathodic protection.
- Tank made of steel clad with a thick layer of noncorrodible material (this option does not apply to piping).
- Tank and piping are installed without additional corrosion protection measures provided that a corrosion expert has determined that the site is not corrosive enough to cause it to have a release due to corrosion during its operating life and owners or operators maintain records that demonstrate compliance with this requirement.
- Tank and piping construction and corrosion protection are determined by the implementing agency to be designed to prevent the release or threatened release of any stored regulated substance in a manner that is no less protective of human health and the environment than the options listed above.
UST systems must also be designed, constructed, and installed in accordance with industry codes and standards and according to manufacturer’s instructions.
UST systems installed before December 22, 1988 must be protected from corrosion. These USTs must meet one of the corrosion protection standards listed above or meet one of the upgrade options described below (or be properly closed):
- Interior lining.
- Cathodic protection.*
- Internal lining combined with cathodic protection.*
* NOTE: Prior to adding cathodic protection, the integrity of the tank must have been ensured using one of the following methods:
- The tank is internally inspected and assessed to ensure that the tank is structurally sound and free of corrosion or holes.
- The tank has been installed for less than 10 years and uses monthly monitoring for releases.
- The tank has been installed for less than 10 years and is assessed for corrosion holes by conducting two tightness tests--the first occurs prior to adding cathodic protection and the second occurs 3 to 6 months following the first operation of cathodic protection.
Upgrading bare metal piping is accomplished by adding cathodic protection. NOTE: Metal pipe sections and fittings that have released product as a result of corrosion or other damage must be replaced. Piping entirely made of (or enclosed in) noncorrodible material does not need cathodic protection.
2015 Requirement – Not later than April 11, 2016, all new and replaced tanks and piping must meet the secondary containment requirements, including interstitial monitoring, according to the new requirements for secondary containment. EPA considers piping replaced when 50 percent or more of the piping is removed and other piping is installed. In addition, owners and operators must install under-dispenser containment for new dispenser systems.
Spill Protection
Spill protection is containment around the fill pipe that catches small drips or spills that occur when the delivery hose is disconnected from the fill pipe. This containment is typically called a spill bucket. It may also be referred to as a catchment basin, or spill containment manhole. Basically, a spill bucket is a basin sealed around the fill pipe. To protect against spills, the spill bucket should be large enough to contain what may spill when the delivery hose is uncoupled from the fill pipe. A typical delivery hose can hold about 14 gallons of fuel. Spill buckets range in size from those capable of holding only a few gallons to those that are much larger--the larger the spill bucket, the more spill protection it can provide.
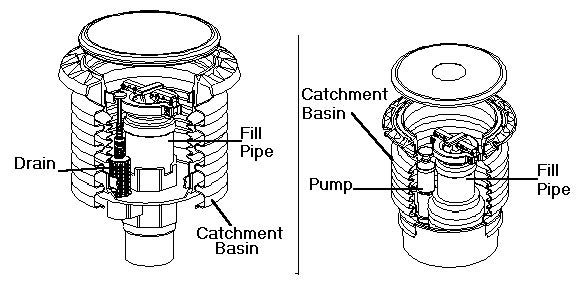
You need a way to remove liquid from spill buckets. Manufacturers may equip spill buckets with either a pump or drain to remove liquid. Or you can purchase a spark free hand pump. You should try to keep your spill bucket clean and empty. Some spill buckets can collect enough water and sediment, along with spilled product, to make draining this mixture into the tank unwise. If this happens, you may pump out the spill bucket and dispose of the liquid properly. If the liquid contains fuel or chemicals, it could be considered a hazardous waste. Contact your implementing agency responsible for hazardous waste for information on testing and handling requirements.
Note: If an UST never receives more than 25 gallons at a time, the UST does not have to meet the spill protection requirements. Many small used oil tanks fall into this category.
Overfill Protection
Overfill protection are devices that either shut off product flow, restrict product flow or alert the delivery operator with an alarm when the tank is close to being full. These devices are installed inside the tank and activate if the product in the UST reaches a certain level in the tank. Typically, your UST must have overfill protection. The three types of overfill protection devices are:
- Automatic shutoff devices.
- Overfill alarms.
- Flow restrictors (also called ball float valves).
Note: If an UST never receives more than 25 gallons at a time, the UST does not have to meet the overfill protection requirements. Many small used oil tanks fall into this category.
What are correct filling practices?
Many releases at UST sites come from spills and overfills that occur during delivery. Although these spills are usually small, repeated small releases can cause big environmental problems. To help prevent spills and overfills during tank filling, the UST regulations require owners and operators to meet the following correct filling practices:
- the volume available in the tank is greater than the volume of regulated substance to be transferred to the tank before the transfer is made; and
- the transfer operation is monitored continuously.
Industry standard practices are also available for tank filling.
Automatic Shutoff Devices
An automatic shutoff device installed in an underground storage tank (UST) fill pipe will slow down and then stop the flow of product to the tank when the product has reached a certain level in the tank. Federal regulations require that shutoff occur when the tank is 95 percent full or before any fittings located on top of the tank are exposed to product. This device has one or two valves that are operated by a float mechanism. The illustration on the left below shows one type of automatic shutoff device. Note that the float is down and the fill valve is open. The illustration on the right below shows the same shutoff device with the float up and the fill valve closed.
Some automatic shutoff devices work in two stages. The first stage drastically reduces the flow of product to alert the driver that the UST is nearly full. The driver can then close the delivery valve and still have room in the UST for the product left in the delivery hose. If the driver does not pay attention and the liquid level rises higher, the valve closes completely and no more liquid can be delivered into the UST, leaving the driver with a delivery hose full of product.
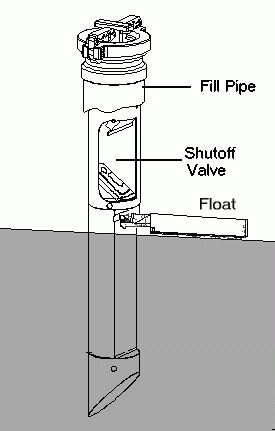
Overfill Alarms
Overfill alarms use probes installed in the tank (see illustration, right) to activate an alarm when the tank is either 90 percent full or within one minute of being overfilled. Either way, the alarm should provide enough time for the delivery person to close the truck's shutoff valve before an overfill happens. Alarms must be located where the delivery person can see or hear them easily. (Overfill alarms are often a part of automatic tank gauging systems.)
Overfill alarms work only if they alert the delivery person at the right time and the delivery person responds quickly. Remember to put the alarm on an electrical circuit that is active all the time so that the alarm will always work. Many deliveries are made at night when the facility is closed. You don't want to turn off your alarm when you turn off the office lights.
Ball Float Valves
Ball float valves (also known as float-vent valves) are fitted on the bottom of the vent line inside the tank. When the product level is below the cage, the ball rests at the bottom of the cage and the vent line is open (see illustration below, left). As the level of the product rises above the bottom of the cage, the ball floats on the product and rises in the cage. As the delivery continues, the ball eventually seats in the vent line (see illustration below, right) and restricts vapor flowing out the vent line before the tank is full. Flow restrictors must begin restricting flow when the tank is 90 percent full or 30 minutes before overfilling. If the tank top is tight, the ball float valve can create enough back pressure to restrict product flow into the tank, which can notify the driver to stop delivery to the tank. However, if the UST has loose fittings or other nontight tank top components, flow will not be restricted and an overfill will occur.
NOTE: Manufacturers do not recommend using ball float valves with suction piping, pressurized delivery, or coaxial Stage I vapor recovery.
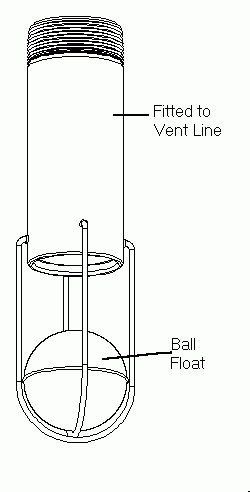
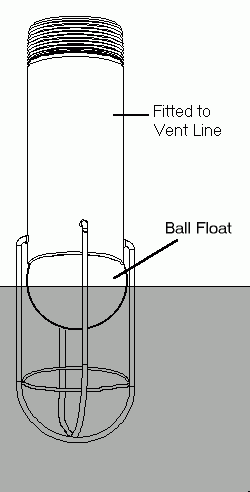
Corrosion Protection
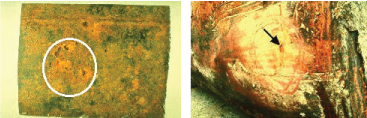
Unprotected underground metal components of the UST system can corrode and release product through corrosion holes. Corrosion can begin as pitting on the metal surface. As the pitting becomes deeper, holes may develop. Even a small corrosion hole can result in significant releases over time. In addition to tanks and piping, metal components can include flexible connectors, swing joints, and turbines. All metal UST system components that are in contact with the ground and routinely contain product must be protected from corrosion. The two common methods used for protecting metal components from corrosion are cathodic protection and isolating the metal component from the corrosive environment.
Overview
All USTs installed after December 22, 1988 must meet one of the following performance standards for corrosion protection:
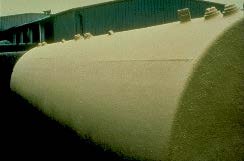
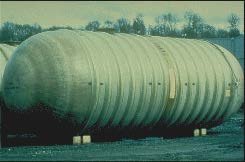
- Tank and piping completely made of noncorrodible material, such as fiberglass-reinforced plastic.
- Tank and piping made of steel having a corrosion-resistant coating and having cathodic protection.
- Tank made of steel clad with a thick layer of noncorrodible material (this option does not apply to piping).
- Tank and piping are installed without additional corrosion protection measures provided that a corrosion expert has determined that the site is not corrosive enough to cause it to have a release due to corrosion during its operating life and owners/operators maintain records that demonstrate compliance with this requirement.
- Tank and piping construction and corrosion protection are determined by the implementing agency to be designed to prevent the release or threatened release of any stored regulated substance in a manner that is no less protective of human health and the environment than the options listed above.
UST systems must also be designed, constructed, and installed in accordance with industry codes and standards and according to manufacturer’s instructions.
UST systems installed before December 22, 1988 must be protected from corrosion. These USTs must meet one of the corrosion protection standards listed above or meet one of the upgrade options described below (or be properly closed):
* NOTE: Prior to adding cathodic protection, the integrity of the tank must have been ensured using one of the following methods:
- The tank is internally inspected and assessed to ensure that the tank is structurally sound and free of corrosion or holes.
- The tank has been installed for less than 10 years and uses monthly monitoring for releases.
- The tank has been installed for less than 10 years and is assessed for corrosion holes by conducting two tightness tests--the first occurs prior to adding cathodic protection and the second occurs 3 to 6 months following the first operation of cathodic protection.
Upgrading bare metal piping is accomplished by adding cathodic protection. NOTE: Metal pipe sections and fittings that have released product as a result of corrosion or other damage must be replaced. Piping entirely made of (or enclosed in) noncorrodible material does not need cathodic protection.
Interior lining
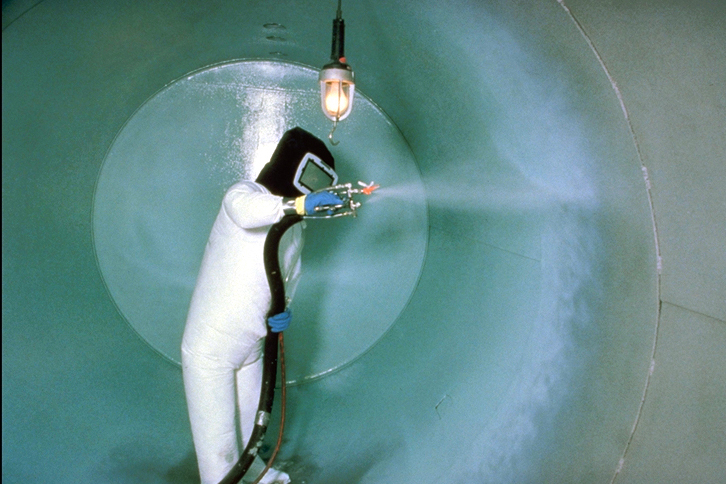
The interior of a structurally sound tank may be lined with a thick layer of noncorrodible material. The lining material and application method must comply with applicable industry codes. The lining used must also meet the same federal requirements as for repaired tanks (40 CFR 280.33). Note: Flexible inner liners (bladders) that fit inside a tank do not meet the tank interior lining requirements. Tanks using only an interior lining for corrosion protection must pass an internal inspection within 10 years and every 5 years after that to make sure that the tank and lining are sound. You should keep records of these inspection results.
Cathodic protection
Cathodic protection is one option for protecting an underground storage tank from corrosion. There are two types of systems for cathodic protection:
- Sacrificial anode
- Impressed current
Sacrificial anodes can be attached to a coated1 steel UST for corrosion protection (see below, left and center). Sacrificial anodes are pieces of metal more electrically active than the steel UST. Because these anodes are more active, the corrosive current will exit from them rather than the UST. Thus, the UST is protected while the attached anode is sacrificed. Depleted anodes must be replaced for continued corrosion protection of the UST.
An impressed current system uses a rectifier to convert alternating current to direct current (see below, right). This current is sent through an insulated wire to the anodes, which are special metal bars buried in the soil near the UST. The current then flows through the soil to the UST system and returns to the rectifier through an insulated wire attached to the UST. The UST system is protected because the current going to the UST system overcomes the corrosion causing current normally flowing away from it.
Federal regulations require that the field installed cathodic protection systems installed at UST sites be designed by a corrosion expert.
The cathodic protection system must be tested by a qualified cathodic protection tester within six months of installation and at least every three years thereafter. In addition, cathodic protection systems must be tested within six months of any repair to any cathodically protected UST system. You will need to keep the results of the last two tests to prove that the cathodic protection is working. In addition, you must inspect an impressed current system every 60 days to verify that the system is operating. Keep results of your last three 60-day inspections to prove that the impressed current system is on and operating properly.
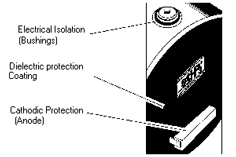
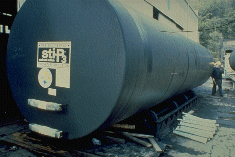
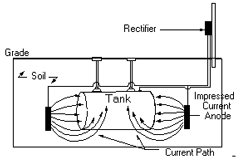
1 The coating must be of a suitable dielectric material (i.e., a coating that electrically isolates the UST from its environment and meets applicable industry codes). An asphaltic coating is not considered a suitable dielectric coating.
Internal lining with cathodic protection
Another option for upgrading existing tanks is to add both cathodic protection and interior lining. If these upgrade options are added at the same time, the advantages of this combined method are: USTs receive greater corrosion protection and the condition of the interior lining does not require periodic inspection.
These advantages can amount to significant cost savings over interior lining alone. However, the cathodic protection system must periodically be tested and inspected to ensure that it is working properly. You must keep records of these tests and inspections.
If internal lining and cathodic protection are placed on an UST at different times, please see EPA's guidance in the UST Technical Compendium in the New and Upgraded Systems section, Question #9, for whether periodic inspections of the lining are needed.